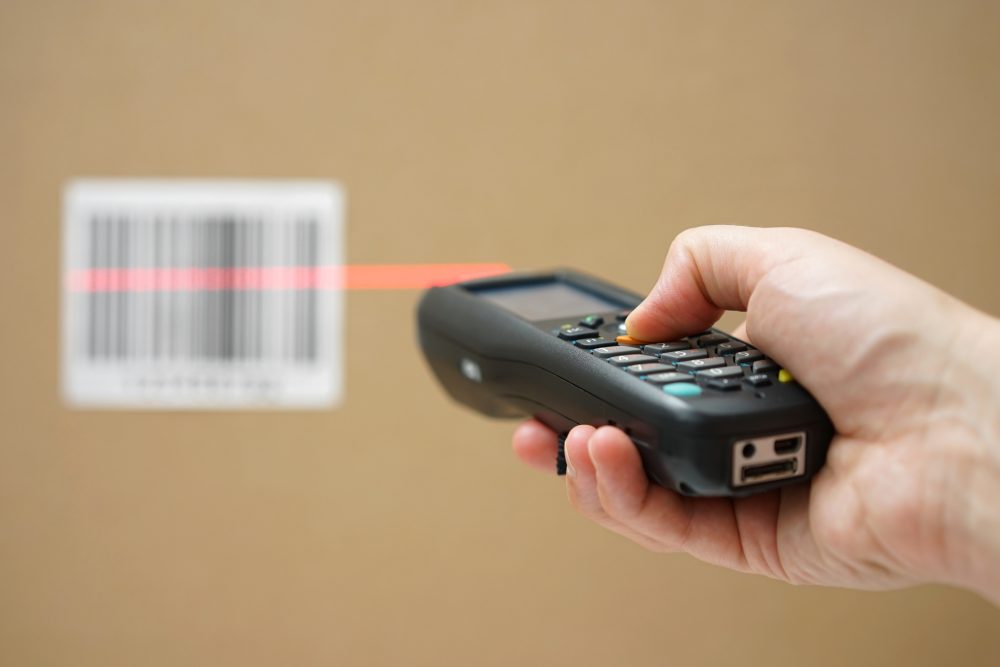
Traceability in the Industry
"Recall because of danger from metal parts", "Car manufacturer calls cars back to the workshop", "Warning because of possible contamination" - consumers are regularly informed about recalls of defective products. For affected companies this is usually associated with high financial expenditure and image damage. But how does it come about? How can quality defects be detected early on? And to what extent can product traceability provide a remedy?
Why traceability is becoming increasingly important
The most common reason for recall actions is that companies recognise quality defects too late and cannot narrow down products and components quickly and precisely enough. What is usually missing is the continuous traceability of all components of products in the production process. Certain industrial sectors such as the electrical industry and the automotive sector are therefore increasingly focusing on the topic of “traceable process safety”.
The goal: Manufactured products must be traceable and identifiable along the entire supply chain, i.e., from delivery, through the individual components, to the finished product. This is the only way to quickly isolate sources of error and defects, and a targeted recall of individual products or batches is efficiently possible.
Traceability – What exactly is that?
Traceability is the ability to follow a trace or track a path, or in short, traceability. According to ISO/IEC/IEEE traceability is defined as “Discernible association among two or more logical entities, such as requirements, system elements, verifications and tasks”. Thus, it is about the traceability of relationships between the work results of a development process.
Especially in areas where standards and guidelines such as ISO certifications (e.g., ISO 26262) come into play, or where safety-critical systems exist, the demand for traceability is very pronounced. For example, in the automotive, medical or food industry.
Traceability in practice
The exact recording, storage, documentation and “relating” of data such as serial numbers, batch numbers, quality data, machine data, conditions, events, quantities, or process data is essential for complete traceability.
From simple monitoring via Excel sheet to intelligent traceability software – companies can draw from a wide range of possibilities. The choice of means must always be carefully weighed up in terms of effort and cost/benefit, because traceability can become overly complex.
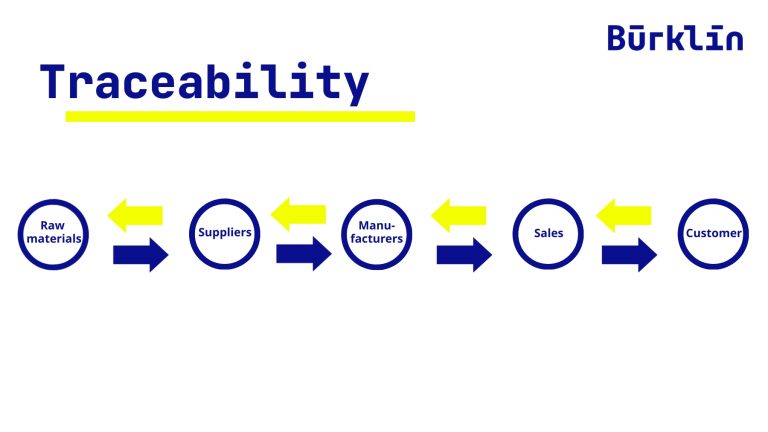
The benefits of intelligent traceability software:
- Increase in quality
- Aautomated and preciseexact recording of process and quality data
- Real-time tracking of the production progress
- fast and precise error analysis and thus reduction of production errors
- Transparency in the supply chain
- legal certainty
The challenges in traceability
Traceability accelerates and improves development activities. It makes it easier to identify changes and their effects and to take countermeasures at an early stage. On the other hand, however, there are the high costs of the effort required to record process data. This is because production and development projects today are increasingly complex in structure and involve large amounts of data that must be organised.
In addition, the data is rarely delivered from a central interface. On the contrary, they are usually created and managed with individual tools. This makes compiling and relating them enormously complicated. Many companies also face the challenges of a complex analysis of the collected data.
Practical example: networked soldering platform WXsmart
Soldering of the future: Weller presented its latest development at Productronica 2019 in Munich: WXsmart. The company is thus setting new standards in intelligent hand soldering technology. Thanks to the connectivity of the soldering platform and the controller via app. Applications that are integrated into a traceability process can be monitored in the best possible way. WXsmart is also ideal for applications that require remote control and monitoring.
Smart Advantages:
- Control and traceability via app and dashboard
- Hhighest connectivity
- Aabsolute security
- Eeasy soldering