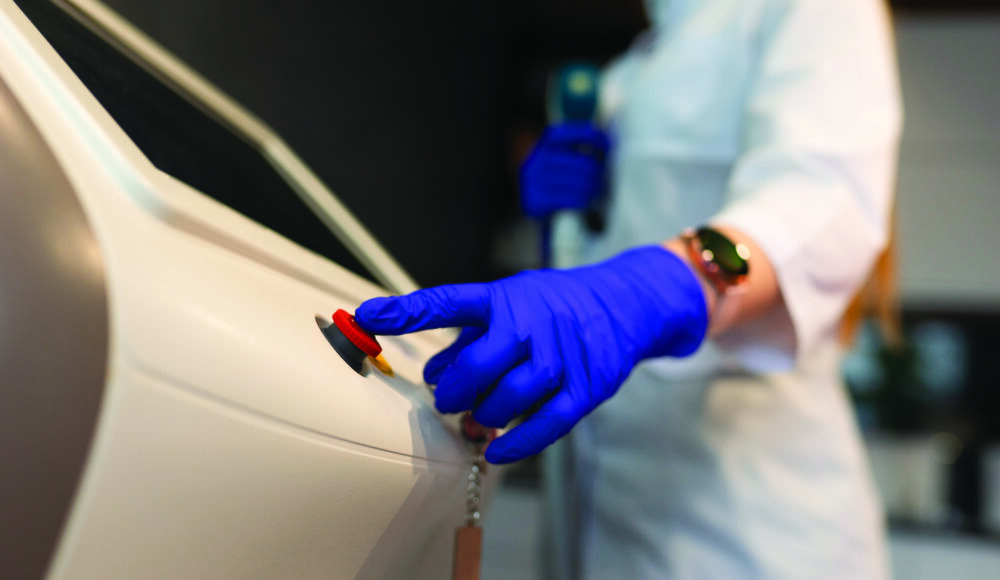
What is an Emergency Stop Switch?
The emergency stop switch is an essential component of emergency control systems, used to immediately interrupt the functions of a machine when necessary. In this article, we provide an overview of emergency stop switches, their applications, and how they work.
Table of contents
- What is an Emergency Stop Switch?
- How Does an Emergency Stop Switch Work?
- Types and Designs of Emergency Stop Switches
- Emergency Stop vs. Controlled Stop (Stop Category 1): The Difference
- How to Connect an Emergency Stop Switch
- IDEC Emergency Stop Switches: Safety with a System
- Standards & Regulations: DIN EN ISO 13850
- Safety at the Push of a Button with Emergency Stop Devices
What is an Emergency Stop Switch?
An Emergency Stop switch (also known as an E-stop switch) is a safety device that disconnects the power supply to a machine or system in an emergency, protecting people and machinery from hazards.
The emergency stop switch is an integral part of safety equipment and is used in a wide variety of electrical systems. The requirement for installation depends on the complexity of the machine: as technical networking and functionality increase, so does the importance and necessity of an emergency stop switch.
How Does an Emergency Stop Switch Work?
The emergency stop switch interrupts the power supply in the associated circuit. By opening the switch, the current flow is effectively interrupted, stopping the machine’s power supply.
The operation of emergency stop switches is deliberately designed to be intuitive and simple to ensure a quick response in critical situations. Bright colours and ergonomic shapes make them easily distinguishable from standard switches.
To restart a machine after the emergency stop switch has been activated, the switch must be manually reset. Only then is the circuit closed again, and operation can resume.
For larger machines, multiple emergency stop switches are installed to allow targeted shutdown of only the affected machine parts if necessary.
Types and Designs of Emergency Stop Switches
Emergency stop switches are differentiated by their shape, actuation method, and triggering mechanism. Typically, emergency stop switches are mushroom-shaped. They are easy to operate in emergencies and can be used even with gloves.
In addition to mushroom-head switches, there are rotary switches, handle switches, pull-wire switches, and lever switches. They are usually operated by hand, but there are also special foot switches.
Emergency Stop vs. Controlled Stop (Stop Category 1): The Difference
In everyday language, the terms are often used interchangeably, but from a technical and normative perspective, emergency stop and controlled stop (Stop Category 1) differ fundamentally:
- Emergency Stop (E-Stop): Immediately interrupts the power supply to a machine. The machine does not necessarily come to a safe position; the primary objective is to disconnect power and protect personnel from hazards. Defined by EN 60204-1.
- Controlled Stop (Stop Category 1): Brings the machine to a defined, safe, stationary state before disconnecting the power supply. This is required when an immediate power-off could cause damage to the system or create additional hazards. Defined by EN ISO 13850 and IEC 60204-1 as a “controlled stop” (Stop Category 1).
Summary: An emergency stop (E-Stop) immediately cuts the power supply whereas a controlled stop (Stop Category 1) safely decelerates and stops the machine before disconnecting power.
How to Connect an Emergency Stop Switch
The connection of an emergency stop switch should only be carried out by qualified personnel. What should be specifically considered?
- Position of the emergency stop switch: It must be mounted in a clearly visible and easily accessible location to ensure quick actuation in an emergency.
- Integration into the circuit: When wiring, the switch is integrated into the circuit so that the current flow is controlled via the switch.
- Panel mounting vs. surface mounting: Panel mounting is particularly suitable for integrated designs, as the switch can be seamlessly integrated into the main control panel. With surface mounting, the emergency stop switches are attached directly to the machine and are often provided with a yellow housing.
Symbols & Circuit Diagrams
In circuit diagrams, the emergency stop switch is represented by an arc on a straight line. In technical documents, this switch is referred to as EMO (Emergency-Off) or ESB (emergency stop button). EMO is mainly used in international contexts.
Resetting & Restarting
After activation, the switch remains locked. To resume normal operation, there are various ways to reset the switch:
- by turning,
- by pulling,
- or with a key.
IDEC Emergency Stop Switches: Safety with a System
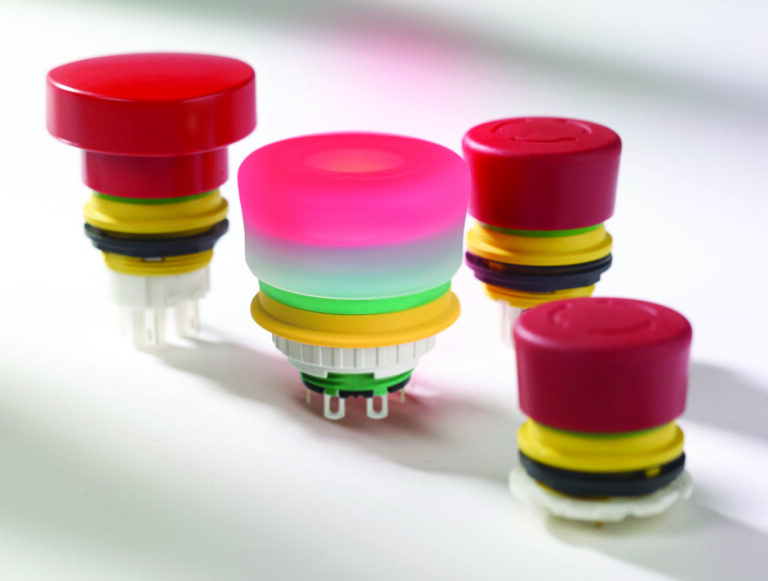
IDEC is a globally recognized manufacturer of high-quality Emergency Stop switches. Notable features include:
- Safe Break Action: A safety mechanism ensuring that the contacts open even when the switch housing is damaged – for maximum safety!
- X6 Series: Compact, hygienic, and robust – ideal for medical or food processing areas.
- XA and XW Series: Various installation diameters suitable for traditional industrial applications.
IDEC switches are modular, durable, and certified according to international standards.
The XW Series from IDEC: Innovation for Maximum Safety
The Emergency Stop switches of the XW Series from IDEC set new standards in safety technology. Based on the revolutionary “Safe Break Action” technology, they offer a unique protection concept: Unlike conventional Emergency Stop switches, which rely on spring force to keep contacts in a closed position, the XW Series uses spring pressure to reliably separate the contacts in case of damage. Even if the switch is damaged or the contact blocks are detached, the circuit is reliably interrupted – preventing injuries and machine damage.
The XW models also stand out for their particularly compact design: With an installation depth of only 48mm behind the control panel and up to four secure contacts, they are perfect for high-safety applications (Level 4).
Another key feature is the new smooth button option, which prevents dirt accumulation – ideal for hygiene-sensitive environments like food, beverage, and pharmaceutical industries.
Practical features such as a visible green status indicator for remote monitoring and flexible reset options (via turning or pulling) make operation more intuitive and safe. The robust, IP65-rated switches are certified to international standards such as ISO 13850:2015, IEC60947-5-1, and UL NISD, and can withstand extreme conditions in emergency situations.
The IDEC XW Series offers cutting-edge safety technology – thoughtful, reliable, and versatile.
Standards & Regulations: DIN EN ISO 13850
The DIN EN ISO 13850 standard serves as a binding guideline for the design and implementation of emergency stop and controlled stop functions. The standard ensures safety in mechanical engineering and reduces risk in emergencies. It is internationally recognized and specifically describes the requirements for emergency stop and controlled stop functions.
For emergency stop devices, EN 60204-1 is also relevant.
Safety at the Push of a Button with Emergency Stop Devices
Emergency stop and controlled stop devices are central elements of machine safety but differ fundamentally in their function. Correct selection and installation of these safety devices in accordance with standards is essential to effectively protect personnel, machines, and systems in an emergency. Whether a machine must be equipped with an emergency stop, controlled stop, or both is determined by the individual risk assessment according to EN ISO 12100. Modern solutions from IDEC offer maximum reliability and comply with the latest international safety standards.