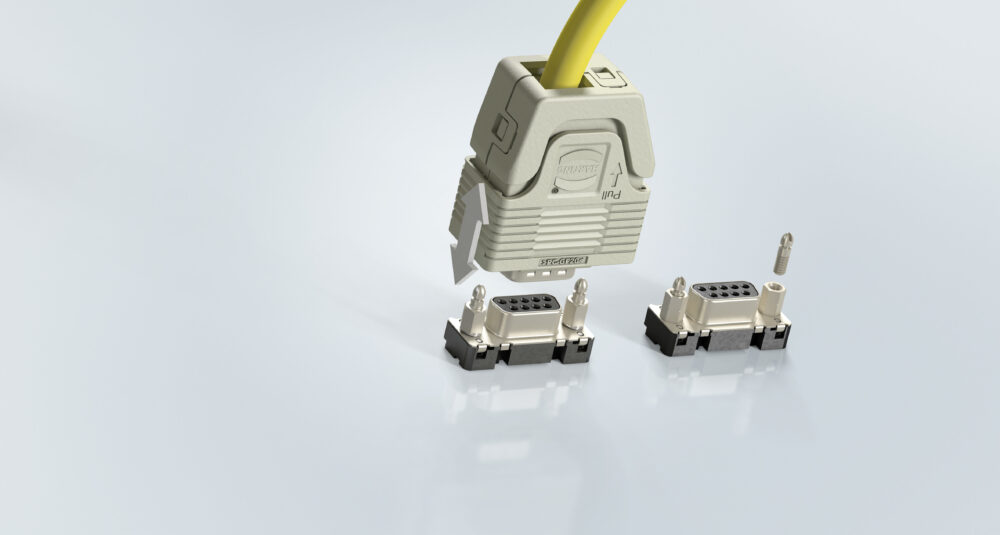
D-Sub Connectors – Everything You Need to Know
D-sub connectors – also known as Sub-D connectors – have been a staple of electronic systems for decades. Whether in offices, industrial environments, medical technology, or even aerospace applications: their versatile design, reliability, and standardization make them a long-standing favourite among connector types. In this comprehensive guide, you'll learn everything you need to know.
What is a D-sub Connector?
A D-sub connector (short for “D-subminiature”) is an electrical connector with a characteristic D-shaped metal shield. This shape prevents incorrect insertion and ensures mechanical stability. Inside the shell, contacts are arranged in two or three rows, allowing for high contact density. The D-sub connector was developed in the 1950s by ITT Cannon and has since become a global standard.
Common variants include:
- 9-pin (DE-9)
- 15-pin (HD-15)
- 25-pin (DB-25)
These connectors are available as both male and female versions and are often integrated into front panels of devices.
What is a D-sub Port?
A D-sub port is the physical interface on a device that receives the D-sub connector. It consists of a housing opening with either a female or male connector and serves to transmit electrical signals between devices safely and reliably. These ports are often soldered onto printed circuit boards and screwed to the device to ensure a secure fit even during vibrations or movement.
They are commonly found on:
- PCs, laptops, and industrial controllers
- Measurement and testing equipment
- Power supply and networking hardware
- Medical and laboratory devices
Applications of D-sub Connectors
D-sub is used globally across a wide range of industries:
- Computer technology: VGA, serial ports, debug interfaces
- Industrial automation: controllers, sensors, actuators
- Medical technology: imaging, diagnostic equipment, patient monitoring
- Aerospace: robust connections under extreme conditions
- Military technology: communication, navigation, weapon systems
Key advantage: The connection is simple, standardized, mechanically secure, and available long-term.
What Types of D-sub Connectors Exist?
There is a wide variety of D-sub connectors. In addition to different pin counts, there are also variations in density and form factor:
- Standard Density (STD): e.g., 9, 15, 25, 37 or 50 pins in 2 rows
- High Density (HD): e.g., 15, 26, 44, 62 or 78 pins in 3 rows
- Mixed Layout: combines signal, high-power, and coaxial contacts
There are also versions for different mounting types.
Is D-sub the Same as VGA?
This question arises frequently, as the terms are often used interchangeably. Technically, they refer to different things:
- D-sub refers to the physical connector (e.g., HD-15)
- VGA refers to the transmitted signal (Video Graphics Array)
The VGA interface uses a 15-pin high-density D-sub connector, which is why the terms are often confused.
HARTING PushPull: The Modern D-sub Solution for Industrial Applications
A standout innovation among modern D-sub connectors is HARTING’s new PushPull locking generation. It combines the proven D-sub technology with an innovative locking mechanism that enables fast, tool-free, and secure connections – ideal for industrial applications with high demands on efficiency, safety, and future-readiness.
The PushPull models are resistant to vibration and shock (IEC 61373 – Cat. 1, Class B), backward-compatible, and available in various housing sizes (09, 15, 25). Thanks to mechanical coding with up to 36 variants, flexible cable entry, and easy retrofitting using “upgrade pins,” existing systems can be expanded effortlessly.
Whether for classic interfaces such as RS232, PROFIBUS, CAN-BUS, or modern mixed D-sub configurations – the PushPull version offers a practical solution for industrial communication.
Advantages of HARTING’s D-sub Connectors: Easy Retrofitting and More
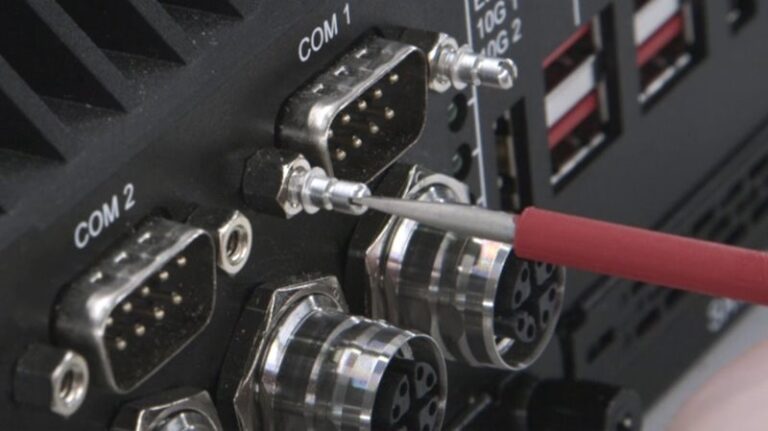
The innovative locking system allows for simple and effective handling. It works via two springs that latch into special locking bolts, preventing accidental disconnection. When the housing is pulled back, the system releases, allowing the connector to be removed effortlessly.
These locking bolts are central to the system and greatly facilitate retrofitting of existing D-sub connections.
In addition to the proven PushPull mechanism, the hood has been enhanced with new functions. Customers can now integrate D-sub coding frames into hoods with an additional slot.
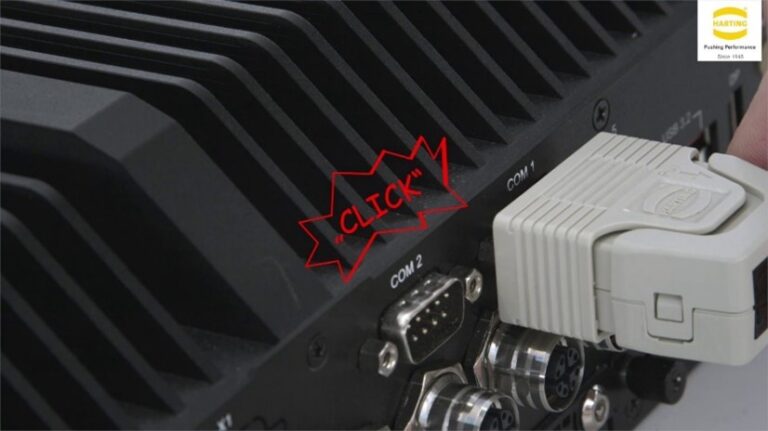
This allows mechanical coding of up to 36 interfaces, preventing accidental misconnection and helping to avoid communication issues or damage to sensitive components.
The D-sub PushPull housings do not require cover screws; after the connector is mounted and the cable connected, the hood simply snaps into place.
To secure the cable, two options are available: a conventional internal cable clamp (included) and an external clamp for larger cable cross-sections, which also offers additional space inside the D-sub PushPull hood.
Rugged Classics with a Future
D-sub connectors are more than just relics of the early computer era. Thanks to their rugged mechanical design, flexible contact configuration, and standardized form, they continue to hold their place in modern technology. Whether as a D-sub housing, a 15-pin D-sub connector, or high-current industrial variants – they offer a reliable, durable connection solution for a wide range of applications.
Discover Bürklin’s wide range of D-sub components, cables, and accessories – available immediately and ideal for your application.