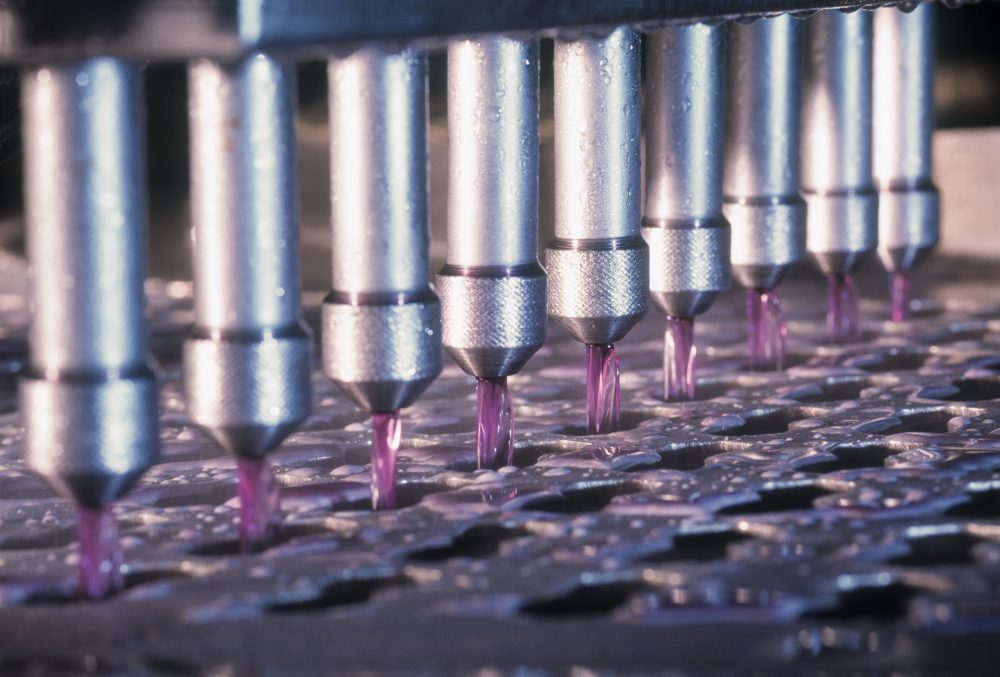
Hygienic Design: Products for the Food & Beverage Industry
What does Hygienic Design mean? Which cables and wires are suitable for use in the food and beverage (F&B) industry? In which areas does the food industry rely on automation technology? It is time to get to the bottom of these and other questions.
Food and Beverage: highest hygiene standards
Hygiene is a top priority in the food and beverage processing industry. Production plants are therefore usually constructed according to the principle of hygienic design. The electronic components used there must meet very stringent requirements. This is the only way to prevent the development of contamination and infestation with germs, and to guarantee the purity of the goods produced.
Requirements for cables and wires for F&B production equipment
What special properties must electronic components have for use in the food & beverage industry? Hardly any other industrial sector places such diverse demands on operating conditions as the production of food and beverages. This is naturally reflected in the use of special cables and wires as well as suitable accessories.
Cold stores, wet rooms, and heat processes: Even under extreme chemical, thermal, and mechanical stresses, electronics must function reliably. Resistance is also important; after all, production facilities are cleaned regularly, accounting for around 30 percent of daily operations. Aggressive acidic and alkaline industrial cleaners are usually used for this purpose.
Whenever cables and wires are in direct contact with food, they should ideally be
- Easily washable
- Disinfectable
- Corrosion resistant
- Non-toxic
- Non-absorbent
- Smooth, continuous, and sealed
It is extremely important to use products that are adapted to the food industry to ensure process safety.
Excursus: The three zones of food and beverage technology
Which lines and cables are suitable for the food and beverage industry also depends on the zone definition of the machines. A distinction is made between three zones that vary in terms of mechanics or temperature due to external influences:
- Hygienic design zone or product zone: The food and beverages are in direct contact with the electronic equipment. Connection solutions are often installed in stainless steel tubes or protective hoses. Examples include cables in mixers or agitators and interfaces to optical sensors for level measurement.
- Splash zone: There is no direct contact with the food. However, drops and splashes can hit the lines and cables in this zone and get back into the food production process. To avoid contamination, for example, robust and versatile special connectors from HARTING that can withstand intensive cleaning are suitable.
- Non-product zone: Since there is no direct food contact, the requirements for cables and wires are not quite as high. Nevertheless, the components should be easily washable, with stainless-steel for housings for example.
As a reminder: the product zone places the highest demands on machinery and electrical components, which is why the choice of the latter should be well-considered.
F&B connection solutions from LAPP Austria
LAPP Austria is the world’s leading supplier of cables, wires, and accessories – offering convincing connection solutions for the highest hygiene standards and diverse applications:
- Milk processing and dairy technology.
- Meat and fish processing.
- Baking and confectionery processing.
- Beverage bottling plants.
- Packaging machines.
The advantages of LAPP connection solutions:
- Temperature-resistant cables and heat-resistant conductors.
- Use of hybrid cables.
- Corrosion resistance.
- Hygienic design conformity.
- FDA approval and certification to EHEDG, ECOLAB® and IPA cleanroom suitability.
Automation technology in the F&B industry
Prevent product contamination. Ensure the safety of consumers and workers. Consider environmental conditions such as temperatures, humidity, or vibrations. Comply with stringent cleaning and rinsing procedures, as well as state and local regulations and laws. Advanced network technology can help meet all of these demands.
Industrial automation is the magic word – and Schneider Electric offers automation technology for areas ranging from manufacturing to plants and food safety to the supply chain. For example, at the machine level, Industrial Ethernet can reduce downtime, improving operational safety and real-time information.
On the subject of improved: Product quality, productivity and profitability can also be increased through automation. Starting with automatic process control, sensors for automatic quality control and vision systems: Important steps towards a sustainable food industry have already been taken.